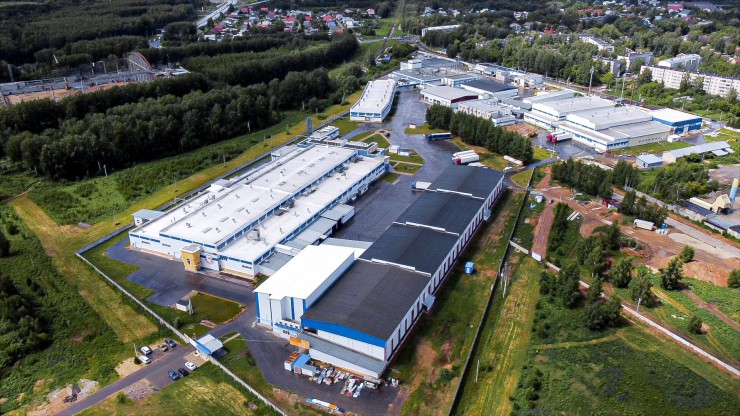
Как меняются подходы к организации складской логистики у одного из крупнейших производителей мороженого — нижегородской фабрики «Колибри».
Сладкая история
«Колибри» — редкий пример семейного стартапа начала 90-х, который не просто выстоял в череде кризисов последних трех десятилетий, но и вырос в одного из лидеров российского рынка. Основатель компании Владимир Николаевич Шибаланский до распада Советского Союза работал наладчиком аппаратов для газированной воды в Сормовском пищеторге, но с началом перестройки предприятие было ликвидировано, а его профессия оказалась невостребованной.
«После девальвации мы стали миллионерами, и у людей не было такой мелочи, которую бы принимал аппарат с газировкой», — шутил Владимир Николаевич.
Оставшись без работы, по совету одного из своих друзей он купил оптом коробку мороженого и повез его продавать в местный клуб, где устраивали танцы. Через несколько месяцев они с зятем Дмитрием Микешиным — сегодня он встал во главе «Колибри» — торговали пломбиром в киоске на рыночной площади, а через пару лет купили польское оборудование и стали производить мороженое сами: по 400 кг в смену.
«Именно мы открыли для всей страны большой рожок, — рассказывает Дмитрий Микешин. — Наши специалисты вручную пекли вафли, сворачивали в рожок. Потом пошли дальше — освоили массовое производство фасованного рожка, упакованного в пленку».
В наши дни «Колибри» выпускает десятки наименований мороженого, вафельных и кондитерских изделий, которое пользуется спросом не только в России, но и странах СНГ. В линейке присутствует пломбир, изготовленный по советской рецептуре 1956 года, — его можно приобрести на Красной площади в Москве. Есть итальянское мороженое ручной работы, которое подают в собственных кафе, и массовый продукт — мороженое, выпускаемое под собственными торговыми марками ритейлеров.
Первые в интралогистике
Сейчас в компании работает около 300 человек. Ежегодно «Колибри» наращивает производство на 15-18%, в летний сезон выпускается порядка 100 тонн мороженого в сутки. Несколько лет назад здесь стартовала масштабная программа по расширению производства. Построен новый корпус, введены в эксплуатацию восемь новейших автоматизированных линий, одна из которых не предусматривает человеческого труда.
«Расширение производства невозможно рассматривать в отрыве от организации складского хозяйства. У нас была задача разместить три тысячи паллетомест на 1,5 тыс. кв. метрах площади», — говорит Дмитрий Микешин.
В качестве партнера по модернизации интралогистики был выбран крупнейший отраслевой интегратор — компания FIRST, с которой у «Колибри» на тот момент уже был опыт успешного взаимодействия в части поставки стеллажей.
C 2016 по 2018 годы специалистами FIRST было возведено два самонесущих склада с общей емкостью 7500 тысяч европаллетомест. Среди их преимуществ — рациональное использование пространства благодаря применению элементов стеллажей в качестве опорного каркаса, снижение капитальных расходов и сжатые сроки строительно-монтажных работ, максимальная плотность хранения грузов и увеличение скорости товаропотока.
«Мы всю зиму производим вафельные изделия, складываем продукцию, проводим сезонное накопление продукта, который лежит 2-3 месяца, а затем забираем его. Новый склад позволил повысить устойчивость к сезонным колебаниям спроса», — комментирует Дмитрий Микешин.
Следующим проектом стала реконструкция склада замороженной продукции с температурой хранения до минус 30 градусов. Рельсовый кран-штабелер FIRST c шаттлом для размещения продукции в канале с последующей отгрузкой без участия человека поднимает паллеты массой до 400 кг, при этой длина рельса составляет 40 м, а глубина линии — 7,5 м. Минимальные размеры доступа в конце прохода, а также в верхней и нижней части пролета, плюс опция безбуферной защиты пролета позволяют полностью использовать пространство для хранения.
«Любой руководитель предприятия, который работает с холодом, мечтает, чтобы у него была холодильная камера, в которую ни один человек не заходит. Благодаря FIRST мы этого добились. Паллет с продукцией сам заезжает внутрь, кран устанавливает ее на определенное место, а когда производится отгрузка на машину — вывозит его, — говорит Дмитрий Микешин. — Важно и то, что автоматизация складского комплекса помогает нам повысить эффективность процесса без увеличения численности сотрудников. Нехватка персонала на рынке труда в Нижегородской области стоит особенно остро ввиду большого числа промышленных предприятий».
На складах и в холодильных камерах мороз часто передается через структуру и спускается до земли, снижая её температуру ниже нуля градусов. Возникают риск пучения земли, промерзания фундамента. При участии FIRST на фабрике «Колибри» была смонтирована система вентилируемого фундамента MODULO. Она предотвращает пучение грунта, убирает излишнюю влажность и обеспечивает высокую грузоподъемность фундаменту.
«Тридцать лет назад мы начинали с того, что мороженое варили в кастрюле, а вафли выпекали на газовой плите. Пломбир продавали в буквальном смысле с колес: сделали — загрузили в машину, ни о каких складах и речи не было. Сегодня интралогистика — это значимый бизнес-процесс, благодаря оптимизации которого мы можем улучшить бизнес-показатели предприятия на 10%, — заключает Дмитрий Микешин. — На чем мы экономить точно не будем, так это на качестве продукта и натуральных компонентах. Хоть страна наша и большая, но рынок мороженого очень тесен и все друг друга знают. А здоровая конкуренция побуждает нас делать вкусное и качественное мороженое».