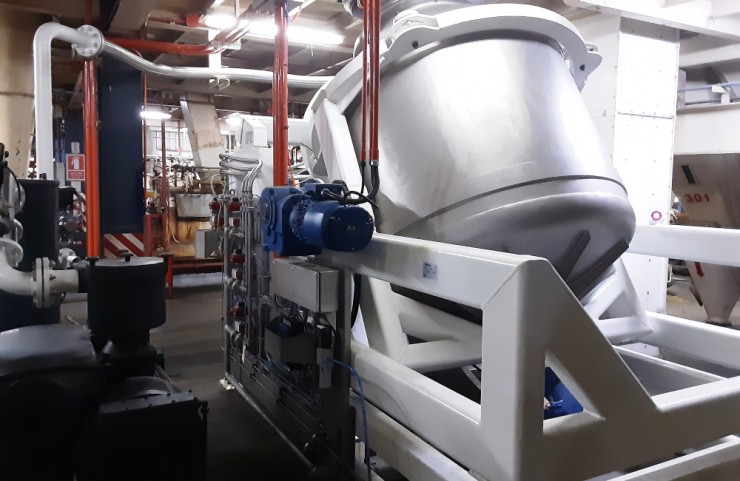
Автор статьи: Штефан Лунгвиц (Stefan Lungwitz), Василий Зябрев, компания Amandus Kahl
С целью ввода жидких добавок при производстве кормов в последние годы широко применяется метод напыления на конечном этапе производственного цикла (PPA - нанесение после гранулирования). Если к гранулам необходимо ввести более 7-8% жидкой фазы, то единственной опцией для этого является применение вакуумного напыления после гранулирования или экструдирования. По сравнению с напылением на гранулы в условиях нормальной атмосферы (шахта обмасливания, смесители), данный метод позволяет ввести на 30-75 % больше жидкой фазы. При вакуумном напылении жидкие добавки не только наносятся на поверхность, но и проникают внутрь гранул по «порам». Так, введение жиров достигает 30-40% при производстве экструдированного корма и 8-10% при производстве гранулированного. Также возможен ввод ферментов и иных активных ингредиентов в небольших количествах либо в естественном виде, либо в виде жидкой смеси.
Процесс вакуумного напыления был разработан в 1990-х годах в Норвегии при производстве кормов для лососевых и теперь, 30 лет спустя, также используется при производстве кормов для скота, птицы и в пищевой промышленности. На сегодняшний день наиболее распространенными типами установок для вакуумного напыления являются двухвальные лопастные смесители и конические шнековые смесители.
Такие конструкций смесителей давно подвергаются критике из-за образования большого количества мелкой фракции и пыли в результате использования агрессивного механического смешивания. Также недостатком такого вида оборудования является невозможность поддержания надлежащих гигиенический условий (налипание материала на лопасти, мертвые зоны) и высокого уровня энергопотребления. Учитывая вышеуказанные аспекты и соответствующие требования рынка, компания-производитель Amandus Kahl подошла к данному процессу с другой стороны и разработала новый принцип вакуумного напыления.
Новая установка Gentle Vacuum Coater (GVC) состоит из смесительного барабана, вращающегося вокруг своей оси в определенных положениях в соответствующих рабочих циклах. Внутри машины отсутствуют какие-либо отдельно вращающиеся механические элементы, что обеспечивает максимальную сохранность продукта, а также минимальный процент разрушения и истирания гранул. Данный аспект крайне важен, так как образующаяся мелочь начинает слеживаться, и ввиду большей площади поверхности материала также возможно связывание большего количества жидкости, что в свою очередь повлечет чрезмерное концентрирование. На крышке смесителя GVC установлены распылительные форсунки для использования до десяти различных жидкостей, кроме того, герметичность при создании вакуума обеспечивается специальным резиновым манжетным уплотнением. При достижении в машине достаточного вакуума (до 50 мбар) жидкая фаза напыляется на продукт, которому в процессе смешивания придается почковидная форма. Далее продукт бережно перемешивается по принципу свободного перетекания (падения). Смесительный барабан разгружается путем вертикального вращения. Помимо прочего, данный процесс с использованием машины типа GVC 1000 был недавно включен в производственный процесс крупнейшим в мире производителем кормов. На производственной площадке в Таиланде данная установка используется для улучшения структуры экструдированного корма для рыб.
Непрерывная эксплуатация на производстве доказала, что при непосредственном сравнении с двухвальным лопастным смесителем установка Gentle Vacuum Coater обеспечивает неизменный уровень качества продукции при снижении процента разрушения гранул и образования мелочи. Анализ эксплуатационных данных показывает, что данная установка имеет огромный потенциал сокращения производственных затрат.
Экономия средств при вакуумном напылении в производстве кормов для аквакультуры
Экономия средств за счет сокращения количества разрушенных гранул и мелкой фракции
Образование мелкой фракции является фактором, влияющим на стоимость продукции, которым нельзя пренебрегать. При производстве кормов для рыбы в Центральной Европе средние затраты на переработанную мелочь составляют 25 евро за тонну. Дело в том, что при так называемом методе сухой переработки мелкая фракция добавляется в продукт согласно пропорциям, на этапе перед измельчением и, таким образом, проходит весь процесс заново. Следовательно, вновь расходуется полный объем механической и тепловой энергии. Кроме того, нельзя забывать про расходы, связанные с износом оборудования, техническим обслуживанием и оплатой труда, а также с потерей производительности, вызванной непосредственно наличием мелочи.
На примере одного предприятия средних размеров по производству кормов для рыбы было подсчитано, что при годовом объеме производства в 80 000 тонн, выход мелкой фракции составляет около 1-3%, которые отсеиваются от готовых гранул.
Причиной образования мелкой фракции, помимо нагрузки на гранулы при прохождении по конвейерам, в основном является механическое воздействие при вакуумном напылении (например, при использовании двухвального лопастного смесителя). Данные 1-3% мелочи из вышеупомянутого примера в числовом выражении составляют 800 - 2400 тонн в год. С учетом вышеуказанной суммы в 25 евро на тонну мелкой фракции затраты данного предприятия на ее переработку составляют 20 000 – 60 000 евро в год.
Испытания показали, что при использовании смесителя Gentle Vacuum Coater (по сравнению с двухвальным лопастным смесителем) образование мелкой фракции при вакуумном напылении может быть снижено в среднем до значения менее 0,1%. Таким образом, потенциал ежегодного сокращения затрат для предприятия очевиден.
Другая проблема - образование мелочи как при транспортировке корма, так и при использовании автоматизированных систем кормления на рыбных хозяйствах. В частности, при использовании системы пневматической подачи корма с транспортного судна на плавучие сетные садки, которая часто применяется, например, в Скандинавии, механическое воздействие на гранулы оказывается особенно сильным. Чрезмерная нагрузка на гранулы в вакуумной установке может привести к образованию микротрещин в структуре гранул готового корма. Такие трещины приводят к дальнейшему разрушению гранул после доставки к заказчику ввиду использования системы пневматической подачи (скорость воздуха > 30 м/с). В результате чего гранулы разрушаются и образуется дополнительная мелкая фракция. Рыба не может это съесть, что снижает коэффициент конверсии корма (FCR). В системах с установкой замкнутого водообмена (УЗВ) такая ситуация приводит к преждевременному загрязнению фильтров для очистки воды. Такие кормовые потери и все сопутствующие расходы обычно значительно превышают суммы из вышеприведенного примера в зависимости от размера рыбного хозяйства.
Так, на средней по размерам скандинавской ферме по разведению лосося, состоящей из 6-10 садков, в день расходуется до 40 тонн гранул корма на сумму приблизительно в 60 000 евро в зависимости от температуры воды. Такие суммы дают представление о масштабе потенциальной экономии для заказчика за счет предотвращения образования микротрещин и в дальнейшем мелкой фракции.
Экономия средств за счет снижения энергопотребления
Кроме того, конструкция новой установки GVC позволяет сокращать энергопотребление. По сравнению с другими установками вакуумного напыления такого же размера, GVC с приводным двигателем мощностью 4 кВт расходует до 80% меньше электроэнергии. Кроме того, в стандартном исполнении все приводные двигатели в системе оснащены частотными преобразователями (установка вакуумного напыления, вакуумный насос, жидкостные насосы), что позволяет сэкономить более 40 % энергии на каждый приводной двигатель.
Экономия средств за счет использования системы автоматической мойки (CIP)
Поскольку напыление производится в конце производственного цикла, к установкам предъявляются высокие требования по поддержанию чистоты и гигиены. По сравнению с двухвальными лопастными и коническими шнековыми смесителями установка GVC демонстрирует хороший уровень самоочищения, поскольку весь объем смесительного барабана постоянно находится в контакте с продуктом. Нет никаких мертвых зон. В случае, если мойка с применением промывочной жидкости все же необходима, например, после использования медицинских препаратов или иных подобных добавок, система оснащена полностью автоматической программой мойки по принципу CIP (мойка без разборки). Особенностью данного процесса является тот факт, что участия персонала для выполнения работ по разборке и очистке машины не требуется. Моющая жидкость на водной основе добавляется автоматически, после непродолжительного процесса промывки автоматически сливается в отдельный слив и утилизируется. Благодаря этому, в значительной степени сокращаются расходы на обслуживающий персонал, а также уменьшается время простоя.
Резюме
В зависимости от условий работы и размера предприятия, метод вакуумного напыления дает возможность сокращения эксплуатационных расходов по многим аспектам. Для каждого предприятия их можно рассчитать индивидуально.