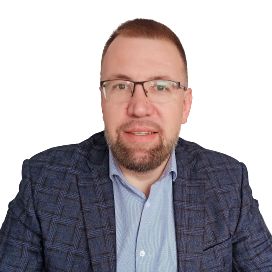
В сентябре 2020 года GEA в России отмечает 5-летие с момента отгрузки первого заказа, выполненного на производственной площадке в Климовске. Владимир Смычников, директор обособленного подразделения ООО «ГЕА Рефрижерейшн РУС», рассказал о том, как с одинаковым успехом производить технологически сложное оборудование для пищевой индустрии и нефтегазовой отрасли и почему важно держать связь с коллегами по всему миру.
— Владимир, как Вы пришли в GEA и стали руководить площадкой?
— В компании я работаю около 13 лет, начинал с должности проектного менеджера. По образованию я инженер-механик холодильных машин, закончил Московский университет инженерной экологии и ранее занимался проектированием систем холодоснабжения.
В GEA меня вместе с коллегами стали вовлекать в крупные проекты из разных сфер: строительство и сборка градирни для охлаждения воды на Краснодарской ТЭЦ, санно-бобслейной трассы в Сочи, предприятий по переработке птицы и КРС компании «Мираторг» в Брянске. Постепенно у нас сформировалась проектная команда.
В марте 2015-го GEA был подписан контракт на изготовление семи дожимных компрессорных установок для Вынгапуровского нефтегазового месторождения. Для реализации этого проекта в компании было принято решение организовать собственное производство в Климовске. По сути, это было продолжение нашей работы по адаптации сборки оборудования к российским требованиям.
— Как такой разносторонний опыт помог команде при строительстве площадки?
— Как говорит генеральный директор группы компании ГЕА в России Оливер Ческотти: «Каждый проект для нас — это управляемое путешествие. Мы всегда изучаем заново технологические процессы, все тонкости и нюансы строительства. Это дополнительная мотивация для развития, и каждый раз это захватывающе и очень интересно».
Прежде чем заняться строительством площадки в Климовске, в течение 1,5 месяцев мы посетили заводы GEA в Германии и Италии, которые выпускали подобное оборудование. При сборке компрессорных агрегатов и холодильных машин мы совместно с коллегами из Южной Африки проводили анализ процессов сборки и затраченного времени. Наш накопленный опыт и опыт коллег очень пригодился. Возможность получить консультации экспертов из разных стран — это одно из серьезных преимуществ нашего концерна.
— Почему в качестве месторасположения площадки был выбран именно Климовск?
— Это одно из самых удобных мест: отличная транспортная доступность —всего 25 км от Москвы. Мы граничим с Подольском — промышленным центром Подмосковья. Правильность нашего решения пять лет назад подтверждает и тот факт, что вся округа сейчас застраивается логистическими складами. Рядом две ж/д станции, аэропорты Внуково и Домодедово, что удобно и для наших заказчиков, которые часто приезжают на площадку.
— Как быстро удалось запустить производство?
— Запуск площадки мы произвели в короткие сроки и, что немаловажно, с малыми инвестициями — менее 500 тыс. евро, хотя проект был начат с нуля. В начале мая въехали на арендованные площади, а в середине месяца приступили к сборке холодильного оборудования для химического предприятия. Параллельно вели монтаж систем электроснабжения, воздушных трубопроводов на самой площадке. К концу июля мы уже были готовы к первому большому заказу — сборке дожимных компрессорных установок.
— Как вы справились с первым заказом? И что было самым сложным в начале работы?
— Для нас это был вызов, наша команда — это строители, а не производственники. Поэтому мы буквально с нуля открывали для себя, как устроен технологический процесс
Первый проект давался непросто. Дожимная компрессорная станция — это контейнер, внутри которого размещается комплекс технологического оборудования с системами жизнеобеспечения: отопления, пожаротушения, газового анализа, видеонаблюдения, удаленного доступа и др. И тут, что называется, пришлось почувствовать разницу: при монтаже холодильного оборудования отклонение в проводке трубопровода в полметра — не проблема. В контейнере же каждый сантиметр на вес золота, важна точность чертежей: ошибка в 2-3 мм может привести к переделыванию узлов. Большую роль сыграла качественная работа наших проектировщиков. В процессе сборки оборудования нам большую помощь оказали наши коллеги из Италии, которые помогали нам своими советами при осуществлении контроля качества выполнения работ на промежуточных этапах сборки. Мы чувствовали себя частью большой международной команды GEA!
В итоге наши установки работают в условиях Западной Сибири уже в течение четырех лет в жестком режиме 24/7 и не вызывают нареканий.
— Возвращаясь к пищевой индустрии: какие особенности у сборки оборудования для производителей продуктов питания?
— В феврале 2016 года мы получили заказ на изготовление пяти автоматических пастеризационных установок для производства напитков и переработки молока. И это был наш первый опыт сборки изделий из нержавеющей стали. Был организован отдельный участок — он должен быть строго отделен от цехов с черной сталью, чтобы избежать электрохимической коррозии. Для такого оборудования предъявляются очень высокие требования к качеству сварных соединений, швы должны быть гладкими и не иметь сильного усиления корня, так как гладкая внутренняя поверхность стенок снижает гидравлическое сопротивление потока в трубе, остатки продукта не остаются на швах, что гарантирует 100%-ю промывку.
Для этого мы закупили соответствующее оборудование, много консультировались с нашими технологами, на первых этапах на производстве находился супервайзер, который контролировал выполнения работ и делился с нами тонкостями и нюансами.
В 2018-м возникла необходимость сборки десяти холодильных установок для охлаждения молока после дойки на фермах. Сейчас линейка значительно расширилась, в Климовске мы выпускаем холодильные машины мощностью от 50 до 360 кВт.
В целом, если говорить о номенклатуре нашей площадки, то 75 % составляет оборудование для пищевой промышленности и 25 % — для газово-нефтяной отрасли.
— Что входит сегодня в эти 75 % и формирует номенклатуру?
— Большой спектр: наша база — холодильное оборудование для молочных предприятий и ферм, мясоперерабатывающих комбинатов и пивоваренных заводов. Также для молочной и пивоваренной промышленности мы собираем пастеризаторы из нержавеющей стали, нагреватели сливок, карбонизаторы, карбоблендеры, пункты приема молока, распределительные гребенки, панели переключения потоков.
Для нефтегазовой промышленности: дожимные компрессорные станции, блоки подготовки и охлаждения газа, сепарационные установки на базе сепараторов и декантеров в блочно-модульном и мобильном исполнении.
Отдельное направление — производство электрощитов для всех направлений нашего концерна. За пять лет работы в Климовске мы выпустили почти 200 единиц различного оборудования, отгрузили более 600 штук электрических шкафов собственного производства. И номенклатура только растет. В настоящее время производственная площадка успешно выпускает порядка 25 видов номенклатуры. Так, в 2019 году объем работ по сравнению с предыдущим годом увеличился на 40 %.
— Но при этом каждый проект — это индивидуальное решение?
— Да, у нас не конвейерное производство, каждый новый проект — это узловая сборка по техническому заданию заказчика со своей индивидуальной документацией, спроектированной нашими инженерами в России.
Кроме того, в Климовске мы сами изготавливаем все металлоконструкции, металлические рамы, узлы трубопроводов. Основные компоненты — компрессоры, декантеры, сепараторы, теплообменники — получаем с наших заводов GEA в других странах, но применяем и комплектующие российского производства.
На площадке проводится проверка сварных соединений, дефектоскопия, испытания на прочность и плотность трубопроводов, общий контроль работоспособности инженерных систем. Кстати, заказчик может приехать на любой этап — приемку конструкций, пневматические испытания, на выходной контроль. Часто у нас проходят и аудиты, причем как коллег из GEA (недавно аудит сепарационной техники проводили специалисты завода из Германии), так и заказчиков. К примеру, одна из крупнейших нефтегазовых компаний привлекает независимых экспертов еще до начала работы, и они контролируют все этапы сборки и, конечно, управление качеством. Такую возможность может предоставить далеко не каждая компания, особенно, если ее производственные мощности находятся за пределами России.
Кроме того, у программистов, которые занимаются разработкой программного обеспечения, есть возможность обкатать программу у нас на производстве до того, как оборудование будет поставлено заказчику. Это позволяет значительно сократить сроки запуска оборудования. Так, последнюю дожимную установку для применения в энергетике запустили всего за две недели, — и получили бонусом заказ еще на три!
— Что представляет собой площадка в Климовске сегодня? Сколько сотрудников работает на ней?
— У нас около 3 тыс. кв. метров производственных площадей, включая офисные помещения, зону хранения и комплектации материалов и компонентов, заготовительный участок, покрасочную камеру, участок сборки электрощитов, участок сборки изделий из нержавеющей стали, сварочные посты и сборочный участок.
Так как производство многофункциональное, вся команда, а это около 50 человек, состоит из специалистов не только высокой квалификация и опыта, но и универсальности. Наши сотрудники умеют практически все, и это дает команде огромное преимущество и возможность реагировать на изменения и трансформироваться под любые задачи клиента.
— Как на работе площадки сказалась пандемия?
— Начну с того, что с первых дней мы были подключены к информационной сети GEA и получали рекомендации от коллег, которые столкнулись с вирусом раньше нас, в том числе на заводах в Китае.
Во время пандемии мы продолжали работать, так как большая часть наших клиентов – это пищевые производства, операционная деятельность которых не останавливалась в этот период. В связи с этим во время работы мы строго придерживались всех гигиенических и санитарных требований.
Эпидемиологическая обстановка в столице и области была сложной, но нам до сих пор удалось избежать случаев заражения сотрудников коронавирусом. Был продуман вопрос с доставкой рабочих, чтобы исключить общественный транспорт, мы развели смены на участках для приема пищи, организовали дополнительную уборку помещений, а также вели разъяснительную работу. И это дало результаты: люди очень ответственно и осознанно подошли к непростой ситуации.
Кроме того, пандемия помогла оптимизировать нашу работу. В рамках компании прошли обучающие программы по оптимизации и увеличению эффективности. У нас многоцелевая площадка, и это дает уверенность, что мы справимся с любыми вызовами. Кризис делает нас сильнее!
— Какие приоритеты в развитии площадки в будущем?
— Планов много. Сегодня мы выпускаем оборудование для четырех из пяти дивизионов концерна и скоро планируем покрыть все потребности. Наше оборудование поставляется на предприятия в России и в страны СНГ, но мы изучаем возможность поставки и за рубеж.
В ближайших планах — перевести участок сборки из нержавеющей стали в отдельный цех, чтобы отвечать требованиям не только пищевой, но и химической и фармацевтической промышленности.
Каждый год растут объемы и увеличивается номенклатура производимого оборудования. В настоящий момент ведутся работы по сборке вентильных станций для холодильных систем пищевых предприятий.
В компании реализуется проект по внедрению новой ERP-системы SAP S/4 Hana, которая позволит существенно увеличить эффективность нашей работы. Мы являемся частью Global Production GEA, куда входит более 50 заводов компании по всему миру. Если какая-то площадка перегружена, мы готовы реализовывать проекты на нашей производственной площадке. При этом уровень качества сборки и профессионализма специалистов должен, как всегда, оставаться высоким — единым для всех заводов GEA независимо от того, где произведено и собрано оборудование — в Германии, Китае или России.